Industry-Leading Service when it matters most
Our foremost commitment in navigating the COVID-19 pandemic is to ensure continuity of services, waste handling safety, and operational excellence for our healthcare partners
COVID-19 Implications on Healthcare Waste Management
Our Commitment to service continuity for Canadian healthcare facilities
Daniels Health is closely monitoring the COVID-19 pandemic to ensure we are in the best position to protect our staff and customers, and ensure continuity of services and operational excellence across our full spectrum of healthcare waste management. Working with the CDC, our compliance experts are keeping up to date with the latest policies and procedures surrounding coronavirus, and consistent with our scientific foundations, we are putting the full force of our infection control approach to work in combatting exposure risk. As the situation evolves, our teams are actively adapting contingency plans to accommodate the unique needs of our customers and the increasing complexities of healthcare services support. Collectively we take very seriously the responsibility to serve healthcare in its time of increased need.
Daniels employs a multi-tiered disaster recovery plan that insures all aspects of our business:
FULL SERVICE
Daniels Health is maintaining a “business as usual” service threshold throughout the current situation. Across our national footprint we have an extensive network of local and centralised talent keeping the lights on and ensuring we maintain waste management service capability and customer support.
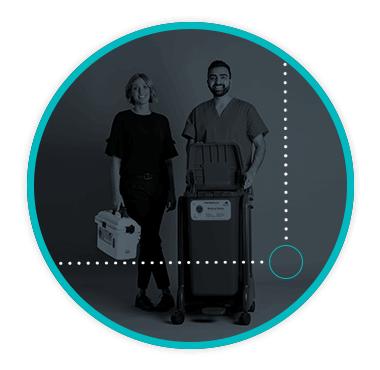
SERVICE CONTINUITY
Daniels’ country-wide footprint is supported by national and global support teams focused on ensuring healthcare service continuity. We have agility of resources and service contingencies in place for increased fluctuations in waste volumes and service scheduling, and maintain a surplus of bins, staff and fleet capacity to accommodate the evolving changes that the Coronavirus pandemic brings.
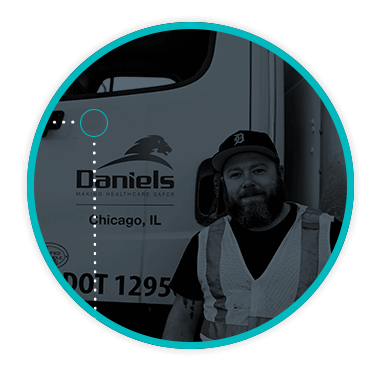
WASTE PROCESSING
Daniels operates a network of processing plants across Canada and the US. This network provides contingency options in the event a plant becomes inoperable ensuring continuity of service. These contingencies were successfully implemented after the 2002 SARS outbreak, and through the implementation of the Disaster Recovery Plan, Daniels was able to manage and maintain service to all customers in the affected areas.
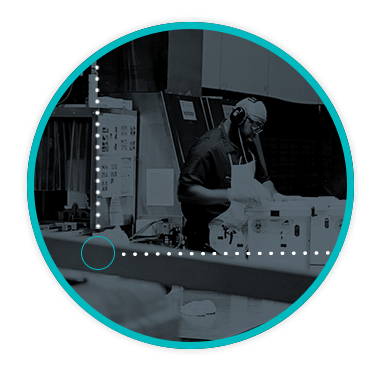
CONTAINER STOCK + DISTRIBUTION
In addition to containers installed onsite at your facility (including spares held in onsite stores) Daniels holds buffer stock at processing plants around the country, and further quantities in our National Warehouse. This provides for increased waste volumes that arise from flu season each year as well as contingency planning for unforeseen events. All our clean facilities have processing capacity, logistical infrastructure and staff resources manage associated volume fluctuations.
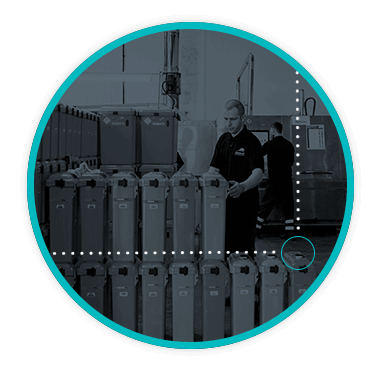
MANUFACTURING + SUPPLY CHAIN
Manufacturing dependency is mitigated by Daniels owning their own set of tools required for the manufacture of sharps and other healthcare waste containers. Outsourcing supply to a number of local manufacturing facilities further mitigates reliance on any single manufacturing arrangement.
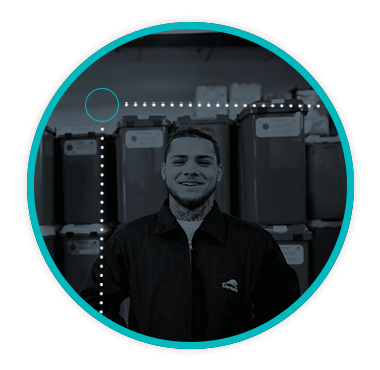
DATA MANAGEMENT
Data and systems are monitored, supported and backed up frequently to a cloud storage system. All infrastructure runs on virtual platforms, meaning hardware failure should not affect our capability to operate. Daniels design/engineering work is maintained in a secure Daniels Engineering Data Management System, which is also backed up to the cloud and accessible remotely.
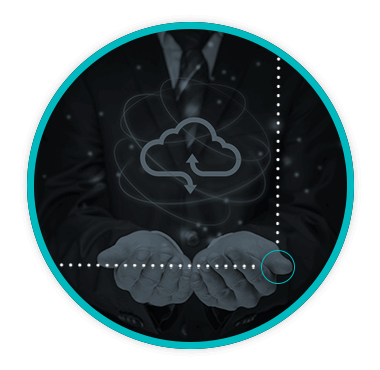
Handling COVID-19 Waste. What you need to know
-
CLASSIFICATION
COVID-19 waste is to be handled and transported as routine UN 3291 cat B waste. No additional procedures, packaging or labelling is required.
-
CRADLE TO GRAVE
Generators are responsible for packaging waste for transport to treatment facilities. Please maintain due diligence when categorizing waste streams to ensure compliance in handling and treatment.
-
YELLOW BAG SECUREMENT
Each bag must be hand tied by gathering and twisting the neck of the bag and using a tie or hand knot to secure the bag, and each container must be securely closed.
-
BIN CONTAINMENT
Closed bags must not be visible once the secondary container (box or reusable bin) is closed. Ensure bins are tightly secured for transport.
COVID-19 Waste Disposal Resources
-
COVID-19 Waste Handling
Providing Daniels Customers with instruction on COVID-19 waste definitions and management for the safety of all downstream staff
Download Here -
Daniels COVID-19 Waste Capabilities
Daniels’ waste management service capabilities and infection-risk-reduction solutions remain unchanged during the COVID-19 pandemic.
Download Here -
Safe Handwashing
5 easy steps to wash your hands thoroughly and prevent the spread of infection
Download Here -
Sharpsmart Reusability
Daniels Sharpsmart containers are reusable; correct handling should ensure they are not disposed of in biomedical waste bins
Download Here -
360L Biomedical Bin Handling
Instruction on how to safely handle the Daniels 360 Litre Biomedical waste bin and yellow liner
Download Here -
Biomedical Waste Disposal
Understand what should be disposed of in a Daniels Biomedical waste tub with simple to use instructions.
Download Here -
How to dispose of COVID-19 waste
A one-page guide on how to properly dispose of and package COVID-19 waste compliantly and cost-effectively.
Download Here
Need a change? Get a resolution. Fast.
-
CHANGE TO SERVICE SCHEDULING
-
ADDITIONAL BINS OR CONTAINERS
-
INCREASED WASTE VOLUMES
-
ADDITIONAL SITES OR PICKUP LOCATIONS
Serving Together
It takes all of us…
Every individual at Daniels Health plays an integral role in ensuring service continuity and quality excellence, from our drivers and field service teams who are on the frontlines of customer service to our national operations team who are working overtime to ensure we deliver the right number of clean containers to our customers each day – we are all here for you. If there is anything we can do better to support your frontlines, please tell us.
COVID-19 RESOURCES
FAQ’s
-
The Centers for Disease Control and Prevention (CDC) has advised that medical waste generated in the treatment of COVID-19 patients and patients under investigation (PUIs) be managed in accordance with routine procedures. There are no additional packaging or transportation requirements from the Department of Transportation (DOT) for biomedical waste or sharps.
-
Yes, we are committed to ensuring 100% continuity of medical waste services, compliance and education, and customer support for our healthcare partners. We are fully aware of the industry’s reliance on our services (more than ever before!) and the vital role we play in supporting patient care. Our teams are united and committed to delivering the highest levels of customer support across our full suite of services.
-
For the safety of our staff and healthcare workers handling medical waste, Daniels is following guidance from the CDC in relation to handling and processing of COVID-19 waste and implementing heightened personal hygiene and environmental cleaning at all Daniels sites. Daniels safety-designed containers are secured with tamper-proof locks to ensure waste is not accessed between the healthcare site and a Daniels processing facility where they are robotically unlocked, decontaminated and sanitised through a robotic washing process that achieves a 10-log microbial load reduction. Our facility based staff are instructed to adhere to any adjustments to infection control protocols and PPE requirements specific to the facility and location being serviced.
-
Daniels Health provides a purchased service, and is not a product supplier effected by supply chain issues with respect to the provision of consumable products on an ongoing basis. Daniels Health has a significant investment in both products and infrastructure required to service the waste management needs of our customers. In addition to the containers physically installed (and excess containers stored at a hospital-facility level), we also hold a minimum buffer of additional spare containers at our processing plants around the country to support. This minimum buffer stock is designed to manage both the increased waste volumes that arise from flu season each year, as well as contingency planning for unforeseen events.
Let’s Talk!
Your time is valuable, and we don’t want to play hard to get. You can either phone us directly on the details listed on our contact page, or feel free to fill out this short form and one of our team members will get back to you as quickly as possible.